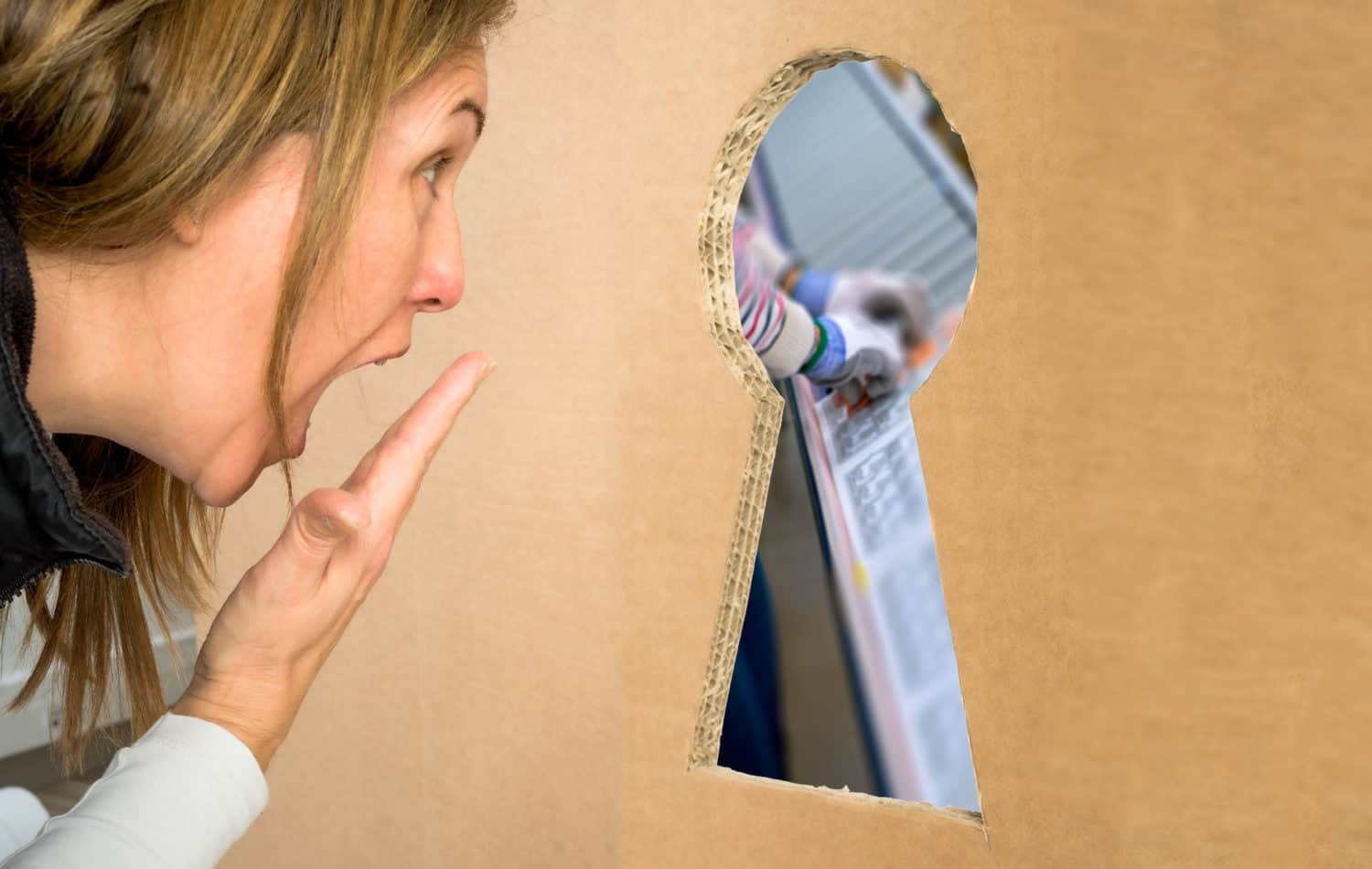
Katia, assembling
Always progressing, Design Duval moved to Sainte-Marie in 2019. In this new 7500 m² workshop, we merged our two production sites so as to meet our customers needs as closely as possible and optimise our processes. We are proud to have a modern and efficient welding, thermoforming, printing, cutting and assembling machine park, run by more than 50 reactive employees, dedicated to the creation of your “Made in France” product.
We use no less than nine different production and printing techniques to produce your sample displays, promotional packaging and welded leather articles, separately or combined. The choice of techniques is made according to your requirements and the use of the final product.
Our production techniques
High frequency (HF) welding
HF welding is a process for joining two or more thermoplastic sheets positioned between two electrodes energized at high frequency. The welded area matches the shape of the tooling used.
PVC being available in different thicknesses, tints, textures, grains, colours (including transparent or translucent) which can be reinforced (with cardboard, PP, wood…), HF welding makes it possible to produce a wide variety of products:
High frequency welded products can be fully customized:
- by cutting simple or complex shapes,
- by printing: offset, digital, screenprinting, gilding..,
- by adding accessories: latch, eyelet ..,
always aiming to provide you with a unique and entirely bespoke product.
At Design Duval, pioneer of HF welding in France in the 60s, we value this process for its many qualitative advantages (fast, non-polluting, precise, resistant welds…) but also for its innovative potential!
HF welding can also be combined with thermoforming to create sample display cases for example.
Thermoforming
With thermoforming, you can create a 3D object from a plastic sheet using heat, a vacuum system and tools. The resulting relief shape can be used to display or secure a product.
At Design Duval, we use transparent or opaque thin thermoforming PVC sheets, in combination with HF welding, to create displays and cases.
Thermoforming has many advantages:
- The price of tooling is moderate in comparison with other plastic processing techniques, such as injection moulding (in some cases, the tooling can even be reused and adapted to a possible evolution),
- quick to set up,
- suitable for small and medium series.
We chose to add thermoforming to our many skills in the 80’s to satisfy our creative needs. Mastering this process opens a wider range of possibilities to create affordable, highly flexible and reactive sales aid products.
Laminating / Turn-in
Lamination refers to the gluing together of several layers of paper and/or cardboard. Design Duval creates displays and promotional articles out of compact cardboard laminated with a sheet of paper.
Four-colour printed and laminated paper, textured decorative paper, leatherette, cork imitation… there are many options! With the lamination technique, an unlimited number of choices are possible to customize and finish your products.
Design Duval provides :
- Lamination alone: a sheet of paper is applied to the front of the cardboard. The edges of the cardboard are therefore visible. This method makes it possible to create rigid backings with rounded corners, in the chosen thickness.
Example of use: cardboard grids in displays, inserted to protect the edges of fragile coating samples.
- Lamination/turn-in: the sheet of paper is applied to the front and covers completely the edges of the cardboard (it “wraps” the cardboard). An end sheet is applied on the back for an impeccable finish. This method is used to manufacture the outside covers of folders, displays, boxes, cases… It also makes it possible to create grids for displays up to 4 mm thick with square corners.
Example of use: sample display folder.
Lamination technique with or without turn-in is intended for professionals wishing to create strong and sturdy displays, folders, boxes, small or large cases… It will fit perfectly into a project with a strong ecological orientation or displaying natural products.
Cutting and folding polypropylene (PP)
Folding the polypro makes it possible to make three dimensional products, in the shape of your choice: suitcases, boxes, folders… To do this, Design Duval
- cuts the PP sheet to the required shape,
- scores the sheet for a clean fold,
- assembles it by snapping, riveting, sticking…
This technique is appreciated for its low tooling cost and the creative potential of the material. Polypropylene can indeed be printed and completed with accessories. It is also available in a variety of colours. Available in opaque, translucent and transparent, PP enables light and transparency effects. A perfect way to give your customers just a glimpse at your products and make them want to see more!
Cutting and gluing techniques
A variety of cutting equipment is available for raw materials (foam, Forex®, PP, etc.) and for cutting samples (aluminium, wood, coatings, etc.) to create all your projects, whatever their shape:
- CNC cutting (milling),
- diamond saw,
- paper cutter,
- heat press.
Our qualified operators use these machines to produce the simplest yet most technical shapes with a perfect finish.
Fitting by gluing the pre-cut shapes together is a competence we have also mastered. A process whick may seem ordinary, but which requires a precise process :
- selecting the highest performant adhesives according to the materials (materials that are often entirely different from one another in terms of quality, thickness, strength. For example, a sheet of leatherette on a cardboard backing or a sample of lime plaster on a PP spacer
- preparing the surface to ensure optimal adhesion,
- high-precision gluing with templates to ensure accurate positioning and alignment,
- pressing the parts together with an exact calibrated press for a perfect fit with no material alteration.
Our printing techniques
Screenprint
Screenprinting is a traditional printing process which consists in applying a pattern to a surface by stencil technique. This technique is ideal for high print volume in one or two colours, on
- soft PVC ( covers, folders),
- rigid PVC (boxes, POS),
- thermoformed PVC (display),
- polypropylene (boxes, cases, binders)
or to customize leatherette, nylon, EVA pockets and cases… Screenprinting is great for the flexibility of its print materials, the durability of its colours and its relatively low cost. A protective varnish can be applied. It can also be applied for a tone-on-tone effect. Small series or printing in three or four colours is best with digital printing!
Pad printing
Pad printing is a very old indirect printing method. A pad on which an image has been etched ist impregnated with ink, and applied to the promotional object to be customized. Thanks to the remarkable flexibility of this technique, it is possible to decorate and mark all kinds of materials with difficult shaped surfaces. At Design Duval, we also use it for marking samples (aluminium, wood, etc.).
Pad printing is appreciated for its quick and inexpensive use.
Embossing (or intaglio marking)
Embossing can be used to create a raised or recessed pattern. It can be applied on rather thick, flexible and flat materials (expanded PVC, EVA).
Design Duval suggests that you add colour to enhance the embossed relief or recess. Ideal to emphasize your logo or your brand on your folders, welcome packs, car wallets, organizers, etc…
Gilding
Gilding is the craft of applying a thin coating of gold or silver in the shape of your choice (logo, brand name…) on a surface. Gilding is mainly used to customize high quality cases and portfolios because it gives a shiny and elegant look to your markings. It is an excellent alternative to screen printing.
Inkjet
Inkjet is a non-contact printing process in which micro-droplets of ink are projected from nozzles onto the surface you want to customize. This very simple but high-speed printing technique ensures optimum productivity. It is the ideal way to print references on the back of samples (plaster, tile grout, floors…) made of hard materials:
- aluminium
- Forex®
- injection-moulded PVC
- etc.
Offset
Offset is a printing process based on the principle that water and oil-based inks repel each other. It is the most commonly used method for printing photos, texts, diagrams, etc. Fast, qualitative and inexpensive, it is favoured for mass production printing on a large variety of materials.
At Design Duval, we use it to customize sheets of paper, polypropylene or PVC, that can then be stuck and turned-in on cardboard to make folders, displays, boxes, pockets, or covers… The resulting print can be protected with varnish or lamination (matt, gloss, satin, fabric) for optimum durability. Pantone® colours or selective varnish can be also used for custom-made products… everything is possible! Feel free to tell us what you want!
Digital printing
Digital printing, unlike other printing processes, has no need of a printing form -the part that receives the ink and is used to print. In this case, the computer controls the application of ink to the surface! As no set-up costs are involved, digital printing is inexpensive and favoured to print photographs and pictures individually or in small series.
It can be used on a very wide range of surfaces up to 5 cm thick. Digital printing is particularly suited to the creation of POS displays out of Forex®, Plexiglas, wood, Alu Dibond®, etc.
With this printing technique, we can customize finished products ( customization on request). And we also use it to validate our prototypes.